Development and Rooftop Profiler Test Facility
A new test facility was installed on the roof our building at NPS that allows the profiler to be placed on a 10m long tether cable and have pressure applied allowing the buoyancy engine to be exercised. At least 60 psi of pressure is required to force the ballast fluid back from the external bladder into the internal reservoir (it is not pumped back in to significantly conserve power). This large tube (visible form the moon on a good day) was used to test profiler #2 prior to shipping to the Erebus Tongue field tests, and revealed that the hydraulic oil that we had been using for the last 3 years had degraded and caused the oil to form flocks and blobs that reduced the ability of the hydraulic system to pump oil into the bladder during a buoyancy change. Replacement oil was bought, the system flushed, and the buoyancy engine retested in the lab prior to shipment south.
A fixed-depth instrument package was assembled with the same sensor suite as the profiler - T, S, u, v, w, P and a coherent altimeter using our new ACM board.
Software was developed to sample this instrument from the surface infrastructure package, where it's data, the profiler data, Seacat (deployed at the bottom of the profiler cable), surface GPS, and surface pressure data are locally stored then forwarded via Iridium back home to NPS. The fixed depth flux package will be lowered through the ground return hole on a 8m long set of bolt-together poles that will initially place the flux package 4m below the ice shelf. The upper 4m will freeze into the "ground hole" providing a fixed depth, independent measurement of T/S, current vector and turbulent heat, salt and momentum fluxes immediately below the ice. Since it is surface powered we will sample the current and T/S every 15 minutes, and the turbulent fluxes for 40 minutes every 2 hours. While this system is working the profiler will be used sample fluxes near the base of the mixed layer to determine entrainment fluxes and execute the full cavity current and T/S profiles, typically once a day.
Erebus Tongue Field Tests
Jim Stockel, Miles McPhee and Tim Stanton joined Craig Stevens from NIWA and colleagues at the Kiwi K132 field site at the end of the Erebus Ice Tongue on 22 October 2010 until 7 November. Miles deployed his shallow instrument frame for a couple of days, and a variable depth winched frame to make turbulence measurements from the surface mixed layer down into the weakly stratified pycnocline. The NPS effort focused on deploying and testing several aspects of the profiler in an environment where there were strong currents and easy access to the instrument. This also gave us an opportunity to try out a new, small, light winch that we implemented to replace the large servo winch used at the Windless Bight deployment. The 110volt single phase winch (Figure 3) has a variable speed AC drive and slip rings, and we can change out cable drums in 10 - 20 minutes, which will make the PIG deployments significantly simpler. With the profiler deployed, the fixed depth flux package was deployed 4m below the sea ice and measured mixed layer fluxes for an eight day period with mixed layer temperatures hovering in and out of supercooling.
Having these instruments in the water at the same time and the profiler near the surface provided an important opportunity to inter-compare the profiler, flux package, Seacat CT sensors and Mile's turbulence instruments. We found milli-degree agreement in the temperature sensors, and after initial offsets typical of the toriodal conductivity sensors, 0.004 mS/m agreement in the conductivity sensors during the timeseries, allowing departure from freezing to be estimated to a few mC.
Super-cooled conditions (local temperature slightly below freezing point) were not expected at this site based on earlier observations, but they provided an opportunity to look at the performance of the instruments in these conditions ("unlikely" at PIG) where ice growth can rapidly occur on any nucleation surface. This ice growth limited Mile's shallow frame deployment to two days, and greatly reduced the ability of the profiler cable brake to hold it at a predetermined depth. Fortunately our shallow flux package showed no signs of ice growth on the sensor end, while the back end grew it's share of platelets seen. This growth did not affect the altimeter and it continued to produce clear backscatter profiles that had large returns at the sea-ice interface.
|
The pressurized profiler 'test tube' on the 7'th floor of our building at NPS. The profiler is being winched up for a pressurized buoyancy engine cycle test.
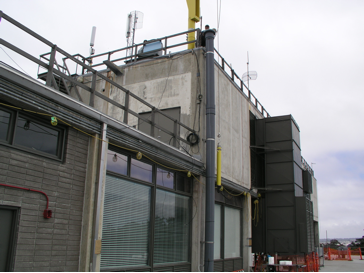 |
|
The fixed depth instrument package after a 10 day test deploynebt in super-cooled conditions through sea ice at the Erebus Tongue field site.
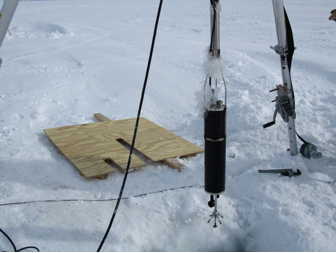 |
|
The new deployment winch being used to support the profiler and SeaCat deployed to a depth of 420m through 2.4m thick sea ice at the Erebus Tongue field site.
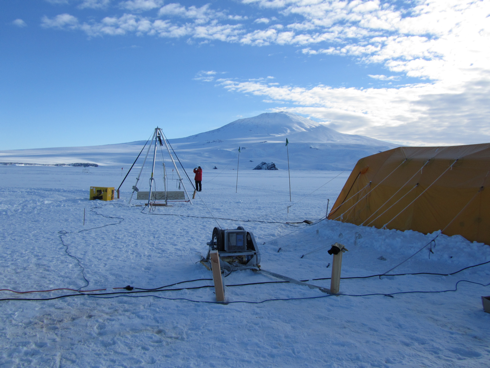 |
|
|